碳热还原法制备氮化硅陶瓷
发布时间:2023-07-06 10:05 浏览人次:1426
碳热还原法制备氮化硅陶瓷的研究进展
摘 要:氮化硅(Si3N4)具有高强度、高硬度、耐磨蚀、抗氧化、良好的抗热冲击性等优点被广泛应用于 机械、能源、化工、航天等领域。目前,生产氮化硅粉体的方法多种多样,由于近年来生产技术的大幅度 提高,以及全球金属矿物价格的大幅度波动,导致采用原料为 SiO2 的碳热还原法生产氮化硅陶瓷被广泛关 注,大量国内外研究人员对碳热还原法生产氮化硅粉体以及该方法结合烧结法生产氮化硅陶瓷进行研究。 因此,总结了该方法生产氮化硅粉体的机制及产出氮化硅陶瓷的特点,并对其研究方向进行了展望。
关键词:氮化硅;陶瓷;碳热还原法;研究进展
氮化硅陶瓷是一种烧结时不收缩的无机非金属材料陶瓷。它不仅具有高强度、高硬度、耐磨蚀、抗氧 化、良好的抗热冲击性等特点,还具有良好的绝缘性能[1-4],被广泛应用于机械、海洋、化工、航天等领域 [5]。要制备具有优良性能的氮化硅陶瓷材料,***先需制备出高纯度、超细粒度的氮化硅粉体。目前市面上 制备氮化硅粉体的方法有很多,主要包括硅粉氮化法、二氧化硅碳热还原法、硅亚胺热解法和自蔓延高温 合成法[6-7]。其中碳热还原法制备氮化硅粉末由于近年来生产技术的大幅度提高以及全球范围内矿石价格的 波动被广泛关注,具有来源广泛、成本低廉、工艺简单等优点,且制得的氮化硅粉体具备高纯、粒细等优 点,是一种适合大批量工业化生产的方法[8]。本文分析了碳热还原法合成氮化硅的机制并对其生产氮化硅 陶瓷的研究进展进行了综述。希望对致力于研究碳热还原法制备 Si3N4 及其陶瓷的工作者给予一定启发。
1 碳热还原合成氮化硅粉体的研究
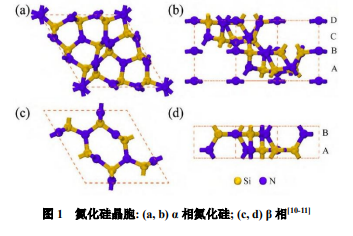
Si3N4 是一种六方晶体结构的无机非金属化合物,含有两种晶型 α-Si3N4 和 β-Si3N4,如图 1 所示。其中, α-Si3N4 是亚稳态的低温相,为六方密堆积结构,β-Si3N4 是稳定的高温相,为似晶石结构,在高温状态下, β 相更稳定,因此 α 相会发生相变转为 β 相[9]。 发生相变转为 β 相[9]。
Vlasova 等[12]研究了在 1673~1723 K 温度及氮流条件下,碳热还原法生产过程中 SiO2 的减少过程。表 明有大量碳核存在时主要生成 α-Si3N4。而在缺少 C 的情况下,熔融液相的 Si-O-N 中间体促进形成 β-Si3N4。 碳热还原法是以碳粉、二氧化硅为原料在高温氮化气氛条件下进行反应。反应为吸热反应,反应温度 为 1481 ℃,反应方程式为: 3SiO2(s) + 6C(g) + 2N2(g)→Si3N4(s) + 6CO(g) (1) (1)反应过程中会涉及到复杂的中间反应,主要有 SiO2(s) + C(s)→SiO(g) + CO(g) (2) SiO2(s) + CO(g)→SiO(g) + CO2(g) (3) C(s) + CO2 (g) →2CO(g) (4) 3SiO(g) + 3C(s) + 2N2(g) →Si3N4(s) + 3CO(g) (5) 3SiO(g) + 3CO(g) + 2N2(g) →Si3N4(s) + 3CO2(g) (6) SiO2(g) + 3C(s)→ SiC(s)+2CO(g) (7) 在进行还原过程中,不同的外部条件可能会产生不同的机制,比如郑彧等[13]研究 SiO2 碳热还原法制 备 Si3N4 是将高纯碳粉与一定纯度的石英粉经细化处理混合后,置于真空炉中,在氮气或氨气环境中,加 热到 1300 ℃以上,此时的 SiO2 先被碳还原出 Si,然后还原出的 Si 与氮气或氨气反应生成 Si3N4。而其他 学者如 Weimer 等[14]认为反应生成的 Si3N4晶体形态与反应物的晶体形态不同,故认为 Si3N4 是由中间产物 SiO 被还原氮化而形成,而非反应物 SiO2。因此,SiO 的生成速率是决定***终产物 Si3N4 生成速率的关键所 在,且表明固-固反应(2)速率快于气-固反应(3)。 也有学者对生产过程的动力学和热力学进行了分析,如陈宏等[15]对 SiO2碳热还原氮化合成 Si3N4 的反 应体系进行了热力学分析,结果表明,Si3N4的生成需要足够高的温度(高于 1800 K)和充足的氮气气氛, 并确定了碳热还原氮化合成 Si3N4 的工艺条件为氮气流量为 3 L·min-1、煅烧温度为 1500 ℃。万小涵等[16] 研究了等温反应下的碳热还原/氮化法合成氮化硅,发现当温度为 1425 ℃时,SiO2完全转化的时间为 7 h; 温度在 1450 ℃时,SiO2完全转化需要 5 h;温度在 1475 ℃时,SiO2完全转化时间为 3 h;温度在 1500 ℃ 时,SiO2完全转化时间为 2 h。这说明反应物 SiO2的还原速率随着温度升高而升高。 Ortege 等[17]进行了动力学分析,认为由于固-固反应仅发生在 SiO2 和 C 有接触的地方,一旦接触处 的 SiO2 和 C 消耗完毕,反应(3)就是生成 SiO 的主要步骤,会影响整个的反应速度。另一方面,随着反应 的进行,生成的 Si3N4会因为晶核作用在 SiO2/C 表面形成一层薄膜层。这时,气相 SiO、CO、N2 的薄膜扩 散速度就会成为影响反应速度的因素。反应(5)是异质核化生成 Si3N4的过程。而气相反应(6)被认为是 Si3N4 晶体生长过程。 还有学者对该方法生产的 Si3N4 晶相进行了细致研究,如陕绍云等[18]通过试验认为反应(2)是由二氧化 硅和活性碳之间的固-固氧化还原反应,产生了 SiO 气态中间产物和 CO。一旦 CO 形成了,SiO 气体就可 以通过气相碳还原反应(3)产生。反应(3)产生的 CO2和 C 通过反应(4)产生的 CO 进一步促进了反应(3)的进 行。接着通过反应(5)和(6),α-Si3N4 晶粒在低温下形成了,随着温度的升高,相转变加速,α-Si3N4 相逐渐 转变成 β-Si3N4 相。 王贻朋等[19]采用 SiO2 和碳粉为原料,N2 作为高温反应气,研究了碳热还原法中反应温度、氮气流量、 原料中碳与二氧化硅摩尔比三个参数对产物 Si3N4 粉体的影响,结果表明:在温度 1600 ℃,氮气流量 1 L·min-1,碳与二氧化硅摩尔比 3.5:1 时,制得的 Si3N4粉体中 α-Si3N4 和 β-Si3N4 含量(w)分别为 58%和 42%。α 相为平均粒径 0.2 μm 的颗粒状,β 相为粒径长 0.5~1 μm 的针棒状。 另外也有学者对该方法生产 Si3N4 的过程中,碳化硅的出现进行了研究。如李虹等[20]认为在氮气参与 的条件下,因为自始自终通有氮气,SiO 气体和氮气发生反应(5),具体为当 N2 充分过量,使 SiO 气体产 生后与之反应生成 Si3N4,则 SiO 分压就达不到生成碳化硅所必需的分压,反应(7)被中断。因此在充分的 氮气氛下,生成碳化硅的反应(7):SiO2+3C→SiC+2CO 实际上无法进行下去。只有当 N2 气的量减少,无 法将产生的气体 SiO 反应掉,而使 SiO 分压升高超过一定值,才有可能通过反应式(7)产生出一定量的碳化 硅。 Liou 等[21]报道了 SiO2 向 Si3N4 转化(见反应式(1))的温度区间为 1350~1475 ℃。当温度高于 1425 ℃时, SiO2的转化率随温度的升高显著增大。他们认为这是由于在此温度区间,一氧化硅(SiO)生成的速度显著增 加。在 1450 ℃时,SiO2 的还原速率在反应开始一段时间后降低。这是由于反应物表面被固相生成物覆盖, SiO2进一步的气-固相还原反应受到了阻碍。他们还指出,温度高于 1500 ℃以后碳化硅(SiC)将出现(见反 应式(7)),并成为主要生成物。 万小涵等[22]研究了碳热还原/氮化合成氮化硅在 1450~1650 ℃、氮气分压 700~1100 kPa 下进行。非晶 二氧化硅与石墨粉末以 n(C)/n(SiO2)=4.5 混合、压片。样品中的氧、氮、碳含量通过 LECO 元素分析仪测 得。反应物和生成物中各物质组成通过 XRD 定性分析。结果表明,通过增加氮气分压,氮化硅的稳定温 度升高,二氧化硅的还原速率随着温度升高而变大。碳化硅的生成仍无法避免。与常压下的碳热还原/氮化 反应一致,高压下的碳化硅和氮化硅的生成亦为连续反应。 随着研究的深入,陆续出现了学者用自然资源代替硅源或碳源来生产 Si3N4 粉体。如姜坤[23]研究以水 玻璃为硅源,预制备出硅酸凝胶后与炭黑进行碳热还原合成亚微米 Si3N4 粉体。并研究加热温度、保温时 间、原料碳硅比以及 N2 流量对整个反应过程的影响。硅酸凝胶中的 Si 是以纳米非晶 SiO2 的形式存在的, 降低了 Si3N4 粉体的合成温度。同时硅酸凝胶疏松多孔的特性大大增加了 N2 与硅及其化合物的接触几率, 所以在低氮气流量下就能完成氮化生成 Si3N4。结果表明,在 1400 ℃氮气流量为 1 L·min-1 的气氛下保温 5 h 能够合成粒度均匀的亚微米级 α-Si3N4粉体,在 1450 ℃时合成了 β-Si3N4 含量为 5%(w)的氮化硅复相粉 体。选择合适的反应温度和保温时间非常重要,温度的高低决定了反应的进行与否,温度一定的条件下保 温时间越长,氮化硅的合成反应就越充分。原料碳硅比对 Si3N4 的形貌有重要的影响,适当的增加碳硅比 有利于合成分散性较好的粉体。
2 碳热还原法-烧结法制备氮化硅陶瓷
目前,市面上制备氮化硅陶瓷的方法主要有反应烧结法(RBSN)、常压烧结(PLS)、热压烧结(HPSN)、 无压烧结(SSN)、二次烧结(PSRBSN)等。其中碳热还原法可以与烧结法结合直接制成氮化硅陶瓷。但是, 这样烧制的陶瓷往往孔隙率较高。这是因为原料中的 C 被反应后,形成的氮化硅填充孔隙而造成的不规则 现象。 碳热还原反应烧结是以 SiO2、C、少量烧结助剂为原料, 在氮气中进行碳热还原反应直接制备出多孔 氮化硅。西北工业大学的鲁元等[24]以廉价的二氧化硅、碳、硅粉为原料,采用碳热还原法-反应烧结法制 备了多孔氮化硅陶瓷。并表明烧结后的试样成分除了少量的 α-Si3N4相和晶间相γ-Si3N4外,其余都是 β-Si3N4 相;通过改变硅粉的含量,制备了不同气孔率,力学性能优异的多孔氮化硅陶瓷。
鲁元等[25]釆用 SiO2和 α-Si3N4在氮气中通过碳热还原-常压反应烧结法,原位反应制备了氮化硅多孔陶瓷。通过改变原料中 α-Si3N4 与 SiO2 和 C 粉的相对含量,可以形成具有细小针状结构的 β-Si3N4 晶粒, 以此获得气孔率可控的高性能的多孔氮化硅材料。随着原料中 α-Si3N4 含量的增大,烧结后,样品的总质 量损失逐渐减小,收缩率逐渐降低,气孔率逐渐减小,弯曲强度逐渐增大。当 α-Si3N4 的质量分数为 50% 时,碳热还原-常压反应烧结的样品中的 β-Si3N4 晶粒具有更高的长径比,样品气孔率为 68.7%,具有优良 的力学性能,弯曲强度达到 37.7 MPa。 Yang 等[26]研究 C 和 SiO2的比例、烧结剂和 α-Si3N4籽晶含量对多孔 Si3N4性能的影响,以 SiO2和炭黑 颗粒为原料,Y2O3为烧结剂,α-Si3N4 为籽晶,压制成形,于 1650~1850 ℃的 N2气氛下烧结制得多孔 Si3N4。 结果发现,C 含量的增加有利于 Si3N4 和 SiC 的形成,适量烧结剂和籽晶有利于 β-Si3N4 生成,使多孔 Si3N4 强度显著提高,其气孔率为 65.0%~71.0%,弯曲强度为 10~37 MPa
Shan 等[27-28]用碳热还原法烧制出孔隙率为 55.47%的高孔隙率多孔氮化硅陶瓷。并表明此法制备的多 孔 Si3N4 陶瓷的主相为 β-Si3N4(β 型晶相呈针状或棒状,其强韧性较好),且不同粗细原料粉末(C 和 SiO2) 会影响陶瓷的微观结构和力学性能,另外不同烧结助剂也会影响微观结构和力学性能。 Luo 等[29]用松木炭作为碳模板, 加入硅溶胶,通以高纯氮气进行反应制备 Si3N4。制备出来的 Si3N4陶 瓷较完整地保持了原材料松木的微观结构。 罗民等[30]以松木炭化后形成的多孔木炭为模板,经 Y2O3/SiO2 混合溶胶浸渍生物碳模板形成 Y2O3/SiO2/C 复合体,在高压氮气氛下(0.6 MPa),1600 ℃碳热还原氮化制备出生物形态多孔氮化硅陶瓷。 并对多孔 Si3N4陶瓷的反应过程和机制进行探讨。结果表明,多孔 Si3N4 陶瓷是由主晶相 β-Si3N4和少量晶 间玻璃相 γ-Si4N4O14 组成;多孔 Si3N4不仅保留了松木的管胞结构,还在孔道中生长出纤维状形貌的 β-Si3N4 颗粒;Si3N4的反应烧结过程包括 α-Si3N4 的形成、晶形转变(α-β 相变)和晶粒生长三个阶段。在 1450 ℃ 烧结的机制是气-固和气-气反应机制,在 1600℃通过液相烧结的溶解-沉淀机制形成纤维状的多孔 Si3N4 陶瓷。 Lu 等[31]用硅藻土作为硅源和 C 粉混合通入高纯氮气进行反应制备多孔氮化硅陶瓷,孔隙率高达 70.1%~79.5%,弯曲强度也有 2.3~14.5 MPa。并发现制备的陶瓷保留了原料中生物质的独特结构。 王雨菲[32]研究了碳热还原反应-常压烧结法制备氮化硅陶瓷工艺,考察了烧结制度、粉料配比以及胶黏剂种类等因素对多孔氮化硅陶瓷的制备的影响。利用 XRD、SEM 以及 MIP 进行了表征,结果表明:制 得的多孔氮化硅陶瓷主要由长柱状 β-Si3N4 晶粒交错搭接形成;1200℃预烧结制度有利于 β-Si3N4 晶粒的发 育和成型,产物长径比较大,组织分布均匀,晶粒结合较为紧密,其内部具备大量不规则孔隙结构,孔容 为 0.554 mL·g-1,气孔率为 48.04%。改变反应物配比制备多孔氮化硅陶瓷,TG-DTA、XRD、SEM 以及 MIP 结果表明:制得的氮化硅主要以长柱状 β-Si3N4晶粒为主,添加 50%(w)的 α-Si3N4的原料配比有利 于 β-Si3N4 晶型的发育和成型,其产物的 β-Si3N4 晶粒均匀,长径比较高,孔隙分布均匀,晶粒结合紧密。 胶黏剂的种类对碳热还原-常压烧结产物没有影响。PVA 相对于 CMC 更能促进晶粒的成长,添加 PVA 后 得到的 β-Si3N4 的长径比更大,孔容、孔径、比表面积以及气孔率都变小,晶粒结合更为紧密,其孔容为 0.142 mL·g-1,气孔率为 22.35%。通过改变胶黏剂可以达到控制气孔率的目的。 以上学者均是对反应物原料中 C 与 SiO2 比值的改变进行研究,发现增加 C 含量可以有效的提高产物 中 Si3N4 的形成。也有学者发现改变烧结助剂硅粉的含量,可以促进多孔氮化硅陶瓷的形成。通过添加适 量 α-Si3N4 籽晶,可以促进 β-Si3N4 的生成,使烧制的多孔 Si3N4 性能显著提高[33]。 3 总结与展望 氮化硅陶瓷具有高强度、高硬度、耐磨蚀、抗氧化、良好的抗热冲击性能,是一种理想的高温结构材 料,加之良好的绝缘性能,使其成为 21 世纪以来耀眼的材料新星,在众多制备氮化硅陶瓷的方法中,碳 热还原法投入成本低、原材料***无害、尾气可循环利用、操作安全性高,容易生产性能优良、多孔隙的 氮化硅陶瓷。但在生产过程一定要控制好原料中碳的含量,克服其生成的粉体含碳、氧高的缺点。***终产 出优质的氮化硅陶瓷。 随着现代社会生产技术的进步与生产资料的扩大化,对于碳热还原法生产氮化硅陶瓷会不断深入,工 艺持续趋于简易,但现阶段碳热还原法还存在许多需要去探索的方向,在此建议以后的研究重点如下: (1)生产粉体的原料中碳与二氧化硅比例的多少。严重影响着氮化硅的转化率,因此笔者认为在进 行生产时,一定要严格把控加入碳粉的含量,将二氧化硅中的氧含量去除而又完美的避免生成过多的碳化 硅杂质。 (2)原料来源的选择。越来越多的实验表明,采用不同碳模板或硅源与多种方法结合的生产方式制 成的氮化硅不仅性能优良,还完美的继承了生物质独特的结构,这些结构是其他制备工艺难以实现的。 (3)添加剂的选择,如:碳粉、α-Si3N4、Si 粉等。为了提高氮化硅陶瓷的热稳定性,我们在生产时 要尽量提高 β-Si3N4 的含量。实验表明,α 相在温度达到 1300 ℃以上时转变到 β 相,使其结构稳定。而 α-Si3N4 作为添加剂在生产氮化硅过程中起着重要作用,作为晶种它可以降低线收缩率,还对成品的孔隙率和弯曲 强度有影响。因此添加 α-Si3N4 含量的多少,如何添加,是否可以结合其他物质进行添加也是一项需要重 点去研究的方向。